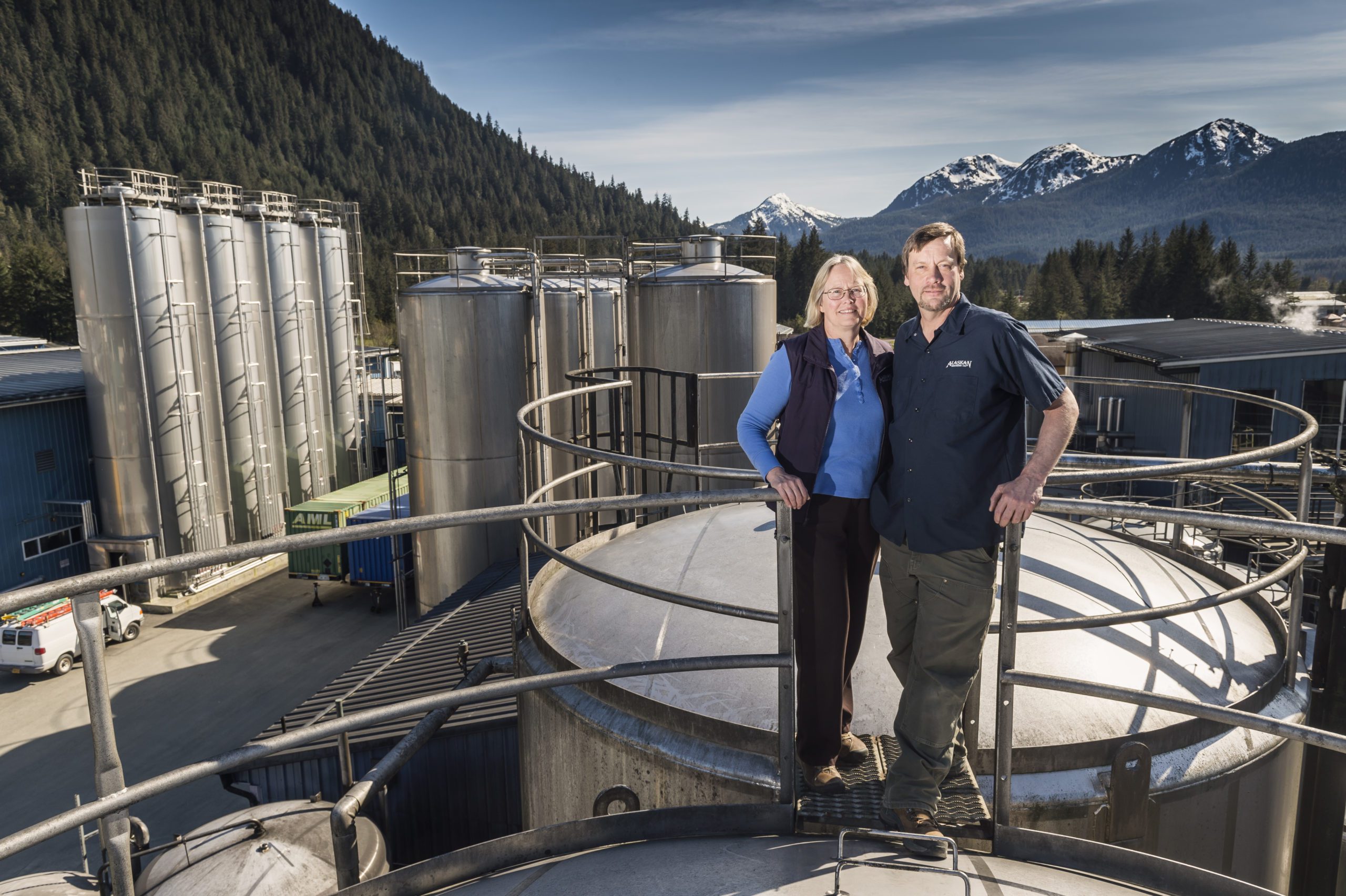
September 13th, 2021 (JUNEAU, AK): Travelling nearly 900 miles across frosty waters, floating metal football fields are responsible for supplying nearly 75% of Juneau-ite businesses with all their supplies. Similarly, these barges are responsible for bringing Juneau’s finest goods to the rest of the world, such as our internationally renowned Alaskan Amber. Yet, despite such isolation the Alaskan Brewing Company has found a way to expand into nearly 26 states competing with breweries with closer proximity to markets, resources and talent in the lower 48.
This is the final part in our 4-part series on “Beer Powered Beer” or the behind-the-scene story of how we at the Alaskan Brewing Company have innovated to compete in distant markets while upholding a commitment to sustainability. This week, we’ll tackle perhaps the most personal and sacred component of our operation: our spent grain steam boiler.
As we related in previous installments, an on-going issue for the brewery had always been our spent grain waste. Unlike breweries in the lower 48, there was nowhere for it to go. Traditionally, grain is sold to local farmers as feed for livestock – however in Juneau, such a market did not exist. In an effort to prevent the landfills from filling up, we were drying our grain, shipping it south, and crossing our fingers it didn’t spoil (as it often did) on the week-long journey to Southern markets.
It soon became apparent we would need to get creative.
What if we could use the dried grain as biofuel? Grain makes great fuel, right? Wrong. Grain CAN be a great fuel. However, a higher density and water content mean it is wildly unpredictable and often inefficient to burn unless it is burned in a very specific set of conditions. Wet grain posed an even bigger challenge.
However, our team was unphased. In an inventive process which would take years of research, trial, error, failure and determination, the Alaskan Brewing team eventually patented a first-of-its-kind process for drying and repurposing the grain as biofuel in 2011.
Using the mash press to first squeeze the grain dry, then further drying it in a proprietary grain drying device (partially grain powered), we were able to create the delicate conditions necessary for a stable burn. This cutting-edge technology not only reduced our oil use by over 65% (reducing operational costs and our carbon footprint), but we believe it that could be implemented by other sustainability-conscious craft brewing operations.
As of today, our brewery operation is proudly carbon neutral providing bold Alaskan brews up to 3,000 miles away.