beer
powered beer
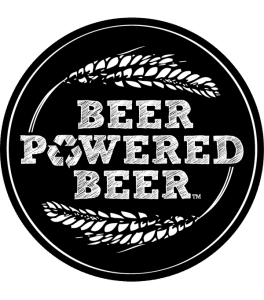
Brewing Brilliance:
Sustainably Crafted, Responsibly Brewed – Beer Powered Beer
At Alaskan Brewing Company, sustainability isn’t just a buzzword – it’s our mission. Since day one, we’ve been pioneers in the craft brewing world, leading the charge in adopting eco-friendly practices. From carbon reclamation to recycling initiatives and reducing fossil fuel and water use, we’re committed to making a positive impact.
What sets us apart? Our innovative Beer Powered Beer process. This unique, closed-loop system is the heart of our sustainable brewing journey, making waves in the craft beer scene across the U.S. We’re not just brewing beer; we’re brewing a greener future.
Why “Beer Powered Beer”? Well, it’s all about using the by-products of our brewing process to power our brewery. We’re not just talking the talk; we’ve walked the walk with six U.S. and international patents and more in the pipeline.
At Alaskan Brewing, we’re pioneers in blending innovation, quality, and efficiency. Our Beer Powered Beer journey involves key players like the CO2 Recovery System (1998), the Mash Filter Press (2008), and the Spent Grain Steam Boiler (2011). These aren’t just fancy names – they’re part of a cycle that makes our brewing not just efficient, but environmentally friendly too.
a positive cycle
Our journey to create Beer Powered Beer isn’t just a process; it’s a commitment to redefining the craft beer industry.
We take our commitment to the environment beyond manufacturing. In 2007, we launched the Coastal CODE (Clean Oceans Depend on Everyone) initiative . This isn’t just a project; it’s a promise to give back. We provide grants to organizations championing beach, lake, and waterway cleanups or working on water habitat restoration.
Being a conscious, community-oriented business is in our DNA. We’re not just making beer; we’re making a difference. From the shores of Alaska to the sunny beaches of California and now stretching to the Gulf and the Midwest, our beer is more than a beverage – it’s a force for good. Join us in raising a glass to sustainability, innovation, and a brighter, cleaner world.
Operating in Juneau has its challenges, pushing us to be more self-sustaining and environmentally conscious.
let's dive into the details
CO2 Recovery system (1998)
We were the first craft brewery in the U.S. to set up a CO2 reclamation system. Instead of releasing carbon dioxide into the atmosphere, we capture and purify it – preventing over a million pounds of CO2 from escaping each year. And here's the kicker: our CO2 comes from renewable, plant-based grains, not fossil fuels.
Mash Filter press (2008)
The first in the U.S. to adopt Belgian mash filter press technology, we found a way to reuse leftover malt grains, reducing our water, malt, and hops usage. Since its introduction, we've saved millions of gallons of water and cut down on diesel fuel and malt consumption. It's not just about sustainability; it's about making better beer with less impact.
Spent Grain Steam Boiler (2011)
Living in Juneau means no nearby farms for our leftover grain. So, we turned our spent grain into a revolutionary fuel source. Our spent grain steam boiler, a first-of-its-kind technology, is fully powered by our leftover grains. Thanks to this innovation, we've slashed our overall oil use by more than 50 percent.